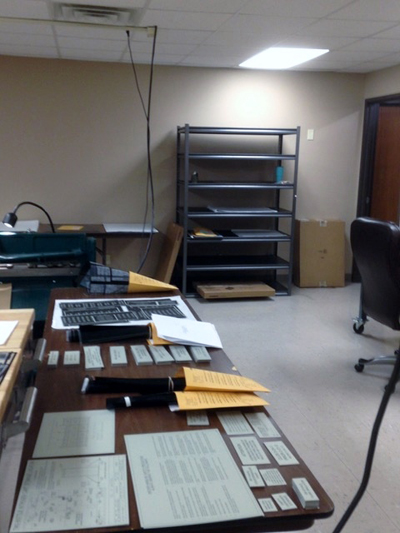
To ensure accuracy, PEC developed a unique organization system: arranging cut tags by size and installation location.
When an order from a government customer for 9,000 Metalphoto® ID tags lands on your desk—for a battleship, nonetheless—you know from the outset that quality and accuracy will be imperative. Thanks to a well-planned manufacturing process and meticulous quality checks, Pella Engraving Company was able to deliver this gigantic order on a tight timeline to a happy end customer.
The variety in this job could have been daunting. Tags ranged in size from one-half-inch square to 20 by 24 inches. Some tags needed only one corner modified, others two—and not necessarily the same corners on each tag. “We only missed one radius corner on one tag,” said PEC Co-Owner Jeff Vroom. “We were very happy with that, and so was the construction company installing the tags on the ship.”
For signage on a battleship, the Metalphoto process is the only option because it uses Phototransfer technology to permanently embed dye into the pores of the aluminum. These tags will stand up to salt water spray and UV rays and will resist abrasion.
To reach this high standard, Pella Engraving invested significant time in planning how the order would be handled. “Organization was crucial to getting all 9,000 pieces manufactured, quality-checked, and shipped in time,” said Jarid Purvis, an artist and etcher for PEC. Jarid built a spreadsheet that divided the tags into small, medium, and large size groupings. Different part numbers indicated the final installation location on the ship: electrical, hull, pipe, or mechanical.
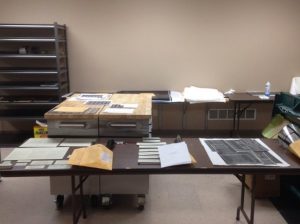
Tags ranged in size from one-half-inch square to 20 by 24 inches, with a variety of corner modifications.
After the tags were cut, they were arranged on tables that had been taped off into sections. After they came back from shearing and corner modification, PEC Co-Owner Cory Vande Kieft checked each tag for accuracy. On tags that needed it, adhesive backing was hand-applied.
“We’re always happy to invest the time needed to make it right for each customer, even if that means adapting or adding to our processes,” said Cory. “With our newly upgraded Metalphoto production area and equipment, we’re now able to offer even more capacity.”
To partner with Pella Engraving Company on your next Metalphoto ID or serial tag project, contact us today!